Proprietary Technology for Cost-Efficient, High-Quality Electronic Component Finishing
Technic's SBE® (Spouted Bed Electrode) is a proprietary, patented electroplating system specifically engineered for high-precision plating of small electronic components, such as connectors, discs, pins, varistors, SMT chip capacitors, and resistors. Leveraging unique design elements, this advanced technology achieves greater efficiency and precision than any other plating method available today.
Our SBE® technology replaces traditional barrel and vibratory systems. It offers a uniquely designed chamber that enables load sizes from 50 to 500 mL, while requiring minimal conductive media. This results in greater plating uniformity across components, significantly reducing common issues such as twinning, coupling, and clumping and enhancing production efficiency.
Technic’s SBE® technology represents a leap forward in quality, speed, and efficiency for manufacturers dedicated to advanced, cost-effective electroplating solutions.
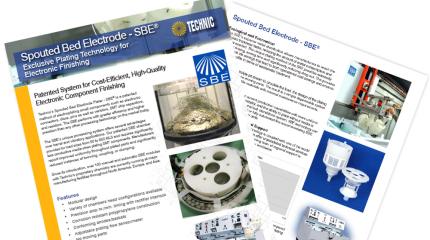
Proprietary SBE Benefits:
- Unparalleled Part Uniformity: Achieves consistent, high-quality plating across each component.
- Reduces Coupling and Clustering: Proprietary technology minimizes typical issues in other plating methods.
- Efficient Media Use: Requires less conductive media, driving down operating costs.
- Enhanced Production Flexibility: Proprietary chamber design accommodates diverse load sizes.
- Operational Savings: Decreases material and operational costs while reducing part damage and waste.